Sanitary napkin machine manufacturers can leverage data analytics in several ways to improve their production efficiency:
- Predictive Maintenance:
- Utilize sensor data from the machines to monitor their performance and condition in real-time.
- Apply predictive analytics to identify potential issues or failures before they occur, enabling proactive maintenance and reducing unplanned downtime.
- Optimize maintenance schedules and spare parts inventory based on predicted maintenance needs.
- Process Optimization:
- Collect and analyze data on various production parameters, such as line speed, temperature, pressure, and material consumption.
- Identify the critical factors that impact product quality, sanitary napkin machine yield, and efficiency using statistical analysis and machine learning techniques.
- Continuously adjust and fine-tune the production processes to maintain optimal performance and minimize waste.
- Quality Control:
- Integrate data from inline quality inspection systems to monitor the consistency and conformance of the produced sanitary napkins.
- Utilize statistical process control (SPC) methods to identify and address any variations or defects in real-time.
- Perform root cause analysis on quality issues to implement corrective and preventive actions.
- Supply Chain Optimization:
- Analyze data on raw material consumption, inventory levels, and supplier performance to optimize the procurement and supply chain processes.
- Develop predictive models to forecast raw material demand and plan production schedules accordingly, minimizing stockouts and excess inventory.
- Identify opportunities for supplier collaboration and inventory optimization to improve the overall supply chain efficiency.
- Demand Forecasting:
- Leverage historical sales data, market trends, sanitary pad making machine and external factors to develop accurate demand forecasts for different sanitary napkin products.
- Use the forecasts to plan production schedules, manage inventory levels, and optimize resource allocation, reducing the risk of over- or under-production.
- Workforce Management:
- Analyze data on labor productivity, absenteeism, and skill levels to identify areas for improvement in the workforce.
- Implement workforce planning and scheduling optimization to match the workforce capacity with the production demand.
- Provide data-driven insights to enhance employee training, job assignments, and performance management.
By leveraging data analytics, sanitary napkin machine manufacturers can make more informed decisions, optimize their production processes, sanitary napkin machine and improve overall efficiency, leading to cost savings, higher product quality, and better customer satisfaction.
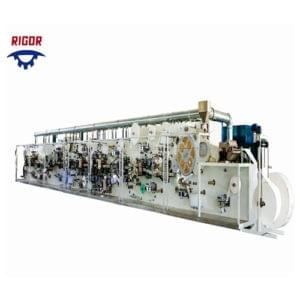