Corrosion resistance in excavator track link assembly materials varies based on the material composition and surface treatments used.
Here are some common materials and their characteristics:
1. Steel Alloys
Carbon Steel: Generally has low corrosion resistance and may require protective coatings or galvanization.
Alloy Steel: Offers improved strength and resistance to wear, but still may corrode without proper treatment.
2. Stainless Steel
Austenitic Stainless Steel (e.g., 304, 316): High corrosion resistance due to the presence of chromium and nickel. Suitable for harsh environments but can be more expensive.
Martensitic Stainless Steel: Offers moderate corrosion resistance with good wear properties, but not as resistant as austenitic grades.
3. Coated Materials
Galvanized Steel: Coated with zinc for enhanced corrosion resistance. The zinc layer sacrifices itself to protect the underlying steel.
Polymer Coatings: Can provide excellent chemical resistance and are often used for added protection in corrosive environments.
4. Composite Materials
Some modern excavators use composite materials that offer resistance to corrosion and are lighter than traditional metals. These materials can be highly resistant to environmental factors.
Factors Affecting Corrosion Resistance
Environmental Conditions: Exposure to saltwater, chemicals, and acidic soils can significantly impact corrosion rates.
Maintenance: Regular inspections and maintenance can prolong the life of track links by addressing early signs of corrosion.
Design and Geometry: Proper design can help minimize areas where moisture can accumulate, reducing the risk of corrosion.
Conclusion
When selecting materials for excavator track links, it’s essential to consider the specific operating environment and maintenance capabilities to ensure optimal corrosion resistance and longevity.
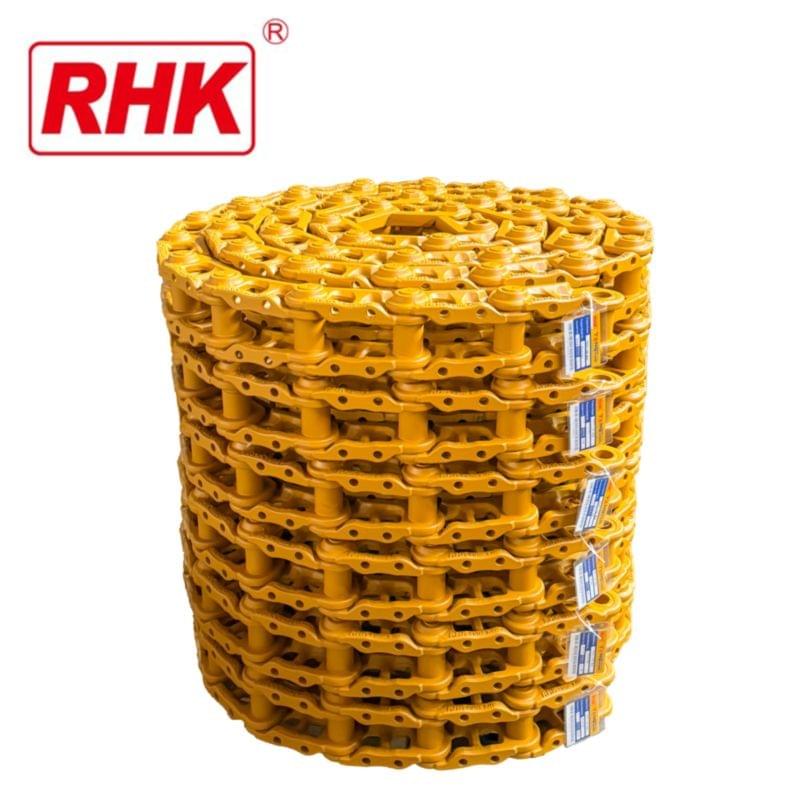