The key parameters that affect the filtration performance of a membrane plate filter press include:
- Membrane Characteristics:
- Membrane material: The type of membrane material (e.g., polymeric, ceramic, metallic) used can significantly impact permeability, selectivity, and fouling resistance.
- Membrane pore size: The pore size distribution of the membrane directly influences the separation efficiency and the size of particles that can be retained.
- Membrane thickness: The membrane thickness affects the flow resistance and the overall filtration capacity.
- Feed Characteristics:
- Particle size distribution: The size and size distribution of the suspended solids in the feed can impact the cake formation, filter press for sale filtration rate, and overall efficiency.
- Feed concentration: The solids concentration in the feed affects the cake formation, compressibility, and the overall filtration performance.
- Feed pH and chemistry: The pH and chemical composition of the feed can influence the membrane surface charge, fouling propensity, and filtration dynamics.
- Operating Conditions:
- Transmembrane pressure (TMP): The pressure differential across the membrane is a critical parameter that drives the filtration process and affects the flux and solids retention.
- Cross-flow velocity: The velocity of the feed flowing parallel to the membrane surface can influence the cake formation, shear, and overall permeate flux.
- Temperature: The feed temperature can affect the viscosity, solubility, and other physicochemical properties, impacting the filtration performance.
- Membrane cleaning methods: The frequency and effectiveness of membrane cleaning (e.g., backwashing, chemical cleaning) are crucial for maintaining the membrane's performance over time.
- Membrane Module Design:
- Membrane configuration: The specific arrangement of the membrane modules, such as flat-sheet, spiral-wound, or hollow fiber, membrane plate filter press can impact the flow patterns and filtration efficiency.
- Membrane packing density: The packing density of the membrane modules within the filter press can influence the overall filtration capacity and operating costs.
- Process Integration:
- Pre-treatment: Effective pre-treatment of the feed, such as coagulation, sedimentation, or screening, can improve the membrane's performance by reducing fouling and enhancing the filtration efficiency.
- Post-treatment: Proper post-treatment of the permeate, such as disinfection or polishing, may be necessary to meet the desired product quality specifications.
By understanding and optimizing these key parameters, operators can enhance the filtration performance, increase the membrane's lifespan, and ensure the overall efficiency and reliability of the membrane plate filter press system.
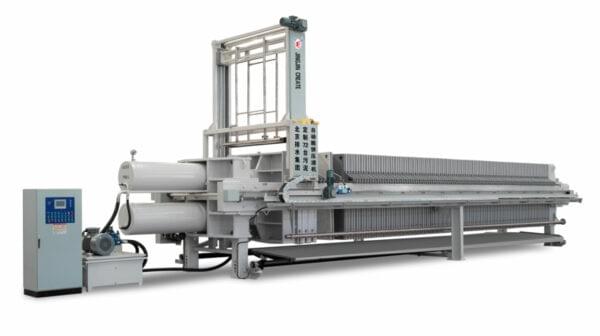